The surface area that fits your cell cultivation needs
Stop operating with a multitude of cell culture vessels to achieve a large growth area. The CellScrew® covers up to 10,000 cm², allowing you to grow adherent cells in a compact vessel without the need for numerous or bulky vessels.

Applications
Cell therapies
Vaccine manufacturing
Seed train
Viral vector production

Less vessels = reduced work load
In cell & gene therapy, manual labor causes up to 71% of production costs¹ leading to cost of up to $4.25 m per dose². Minimize manual labor, space requirements, contamination risks associated with handling numerous vessels and ultimately reduce your cultivation costs and therefore therapy accessability for patients.
Scale with confidence: reproducible results across all stages.
At least three years are needed to get started for a production of adherent cell therapy for clinical development³. The transfer from lab to commercial scale is a time and resource intensive process. We'd like to speed up the process by providing a solution for every step toward accessible therapy.
Available size variants ranging from 850 cm² to 10,000 cm² with comparable process engineering characteristics make it easy for you to scale your cell cultivation process up or down without the need for complex process development.
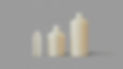

Archimedes’ screws enable excellent mixing and consistent medium supply under low shear forces
Central tube empowers constant flow of liquids and allows for liquid handling using a serological pipette
Concentric cyclinders inside the bottle form a large surface area on a small footprint
The genius in the bottle
The innovative internal structure of the CellScrew® forms a large growth surface on a small footprint and fosters optimal growth conditions with low shear forces and excellent gas exchange.
Constant and homogeneous supply with oxygen and nutrients facilitate cell growth while limiting unwanted cell differentiation.
Efficiently use available incubator space
The CellScrew® requires 92% less lab footprint compared to standard roller bottles. Its extensive growth area within a compact design allows for efficient use of incubator space, reducing the number of vessels needed per batch.

Your team for scaling:
Model | CellScrew® mini | CellScrew® 6K | CellScrew® 10K |
---|---|---|---|
Growth area | 850 cm² | 6,000 cm² | 10,000 cm² |
Media volume | 50 - 120 mL | 250 - 800 mL | 450 - 1,300 mL |
Recommended media volume | 85 mL | 600 mL | 1,000 mL |
Height | 16.78 cm | 19.19 cm | 29.22 cm |
Diameter | 5.3 cm | 12.1 cm | 12.1 cm |
Weight | 120 g | 550 g | 860 g |
Recommended speed | 0.2 to 2 rpm | 0.2 to 2 rpm | 0.2 to 2 rpm |
Mixing times (@ 0.5 rpm) | < 8 min | < 9 min | < 27 min |
kLA (@0.5 rpm) | N/A | 1.95 h-1 | 1.95 h-1 |
Sterilization | sterile (gamma irradiated), not autoclavable | sterile (gamma irradiated), not autoclavable | sterile (gamma irradiated), not autoclavable |
Material | PLA (polylactic acid), TC-treated | PLA (polylactic acid), TC-treated | PLA (polylactic acid), TC-treated |

The CellScrew® combines the advantages of other systems for your adherent cell cultivation
Find out how the CellScrew® compares to your cell cultivation system.
What they both offer:
-
growth surface for adherent cells
Why the CellScrew® improves your adherent cell cultivation:
-
excellent mixing and gas exchange
-
one cultivation vessel with maximized surface
-
small footprint efficiently used
-
easy handling
-
streamlined process


Start cultivating with our bundles.
Resource-conscious cell cultivation
Laboratories are among the most resource-intensive facilities, consuming up to 10 times more energy than office buildings and accounting for up to 60% of carbon emissions in research institutions.⁴
The CellScrew® not only conserves your resources but also those of our planet. Through material-efficient additive manufacturing and the use of plant-based materials, the CellScrew® boasts a 90% lower carbon footprint than other adherent cell cultivation systems.

CellScrew®

Common systems